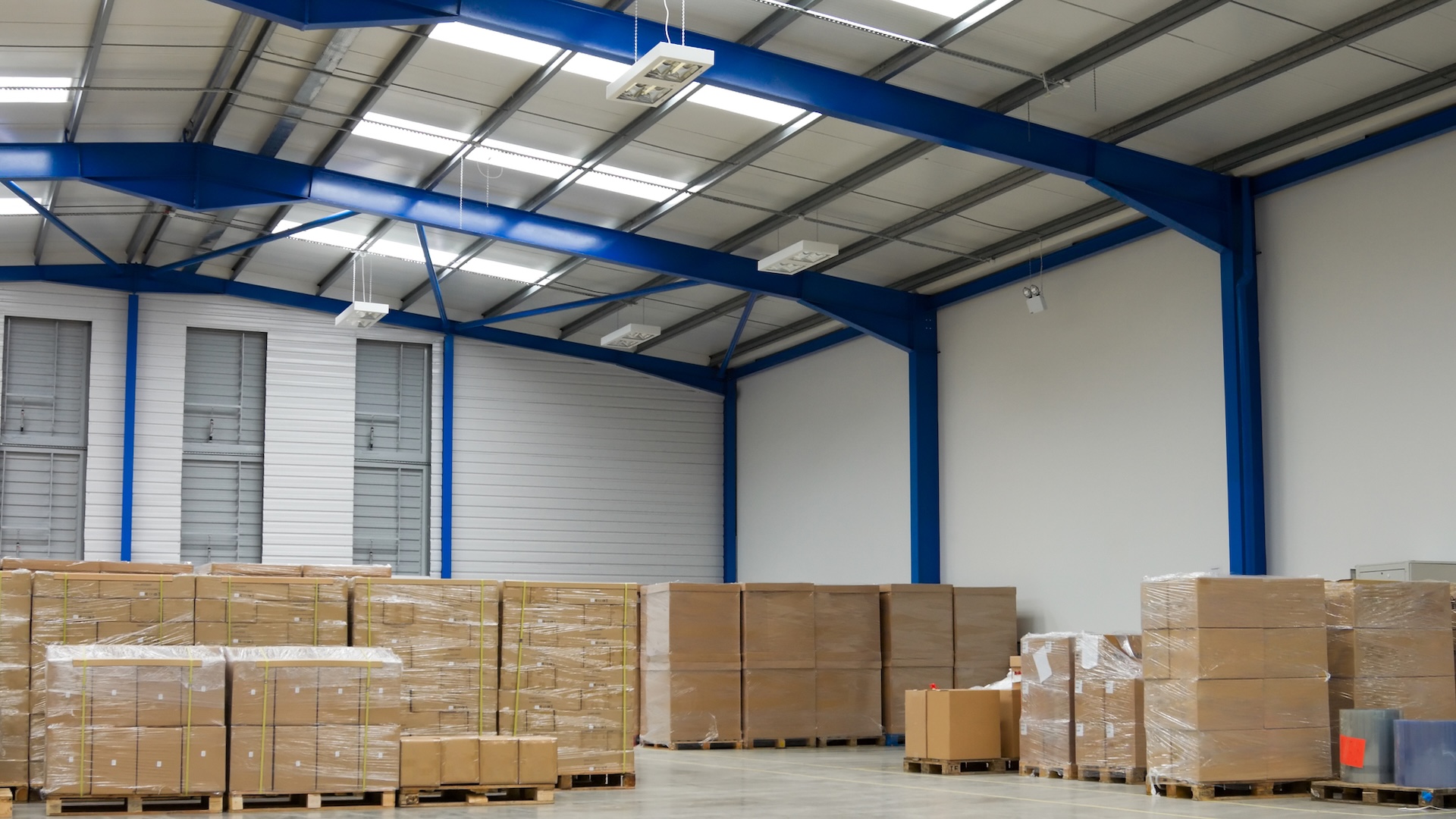
Commercial Metal Roofing Systems Guide
Commercial metal roofing systems have been around for almost 200 years, long before roofs were called ‘systems’. Metal roofs are still the best choice in many climates, presenting advantages over single-ply membrane roofing systems such as TPO and PVC. About one-third of commercial roofs are metal, but there are very few roofing contractors servicing the metal market. Alliant Roofing Company is one of the few.
Alliant Roofing is factory-certified by Metal Sales™ Manufacturing Corporation in Spokane Valley, Rolled Steel Products a Taylor Metal Company in Spokane, and international brand Elevate. We have the equipment, experience, and expertise that many other commercial roofing contractors lack. Alliant Roofing even has its own in-house metal shop to fabricate custom parts, specific to commercial and industrial metal roofing applications.
Commercial Metal Roofing Systems Costs
The initial materials and installation costs are higher for metal roofing systems, ranging from $10 to $20 per square foot. Metal roofs can last between 40 and 50 years with a minimum of maintenance, giving them a total cost of ownership comparable to TPO or PVC. Different metal roof types, panel thicknesses, fastener visibility, and many other factors affect total roofing system costs.
Metal roofs are durable in varying weather conditions and hold up especially well in extreme climates like ours. They are common in large manufacturing facilities and airport hangars, and in circumstances where corrosive chemicals eat through synthetic membranes.
Because commercial metal roofs last so long and are so durable, people often neglect them, resulting in costly leaks. Fasteners (screws and grommets), overlapping panels (laps), and rooftop penetrations are potential failure points with time.
Commercial metal roof leaks are the worst because they trickle. It can take years for building owners to find them. When you finally do find the leaks, the damage is already done. Saturating rains have damaged insulation (lowering r-value), drywall, vaulted ceilings, electrical cables and equipment, plywood and OSB decking. So, when was the last time a roofing professional inspected your commercial metal roof?
One bright spot is the emergence of acrylic coatings that can extend the life of a commercial metal roof by at least 10 years. An acrylic coating service treatment costs about one-fourth the cost of a commercial metal roof replacement, thus making coatings a preferred choice with building owners.
Commercial Metal Roofing Systems Options
Commercial metal roofing systems offer architects and building owners many options, including:
- Roof Slope
- Panel Substrate
- Panel Thickness (Gauge)
- Roofing System Fastener
- Roof Appearance.
Roof Slope
A low slope roof has less than or equal to a two-foot rise over twelve feet horizontally, also known as 2:12. A steep slope roof has more than a two-foot rise over twelve feet horizontally. Steep slope roofs can cost more than low slope because steeper roofs are more difficult to install.
Panel Substrate
Roofing panel substrates include steel, weathering steel, aluminum, and copper. Steel is the least expensive substrate, while copper is the most expensive.
Panel Thickness (Gauge)
Commercial panel thicknesses range from 29 gauge to 22 gauge, also known as medium weight.
Roofing System Fastener
The three most common types of commercial roofing fasteners are standing seam, exposed fastened and concealed fastened.
A Standing Seam Roof has interlocking panels that require no through fasteners.
An Exposed Fastened Roof has through fasteners that are visible after installation.
A Concealed Fastened Roof has through fasteners that are hidden from view after installation.
Roof Appearance
Many commercial metal roofs are architected to be seen from street level. Color, finish, and panel style play key roles in blending the roof into the architect’s overall design. Replacing a faded, aging metal roof can fix persistent leaks and restore your building’s vitality.
Steel roof panel finish is typically Galvalume®, an aluminum-zinc alloy coated steel. Weathering steel and copper panels might have no coating options at all.
What Goes Under A Commercial Metal Roofing System?
What goes under a commercial metal roofing system depends upon the roof deck structure: open frame or solid substrate. An open frame roof can require nothing more than purlins (mounting points) between the roof panel and trusses/structure frame. A solid substrate roof deck can require insulation board and high-temperature underlayment beneath the roof panels. Revised building codes might require sheathing for an open frame metal roof replacement, too.
Metal Roofing Systems Much Harder To Repair Or Replace
Knowing when to repair or replace a commercial metal roofing system is much harder than a comparable membrane roofing system, especially when ordering full-length metal roof panels and navigating revised building codes. Alliant Roofing Company guides architects and building owners to the best outcomes for their commercial metal roofing systems. Call Alliant Roofing’s manufacturer-certified, metal roofing experts today at 1-833-228-8622 to discuss your next commercial metal roofing project and schedule a free inspection.
Citations
- Alliant Roofing – Ribbed Metal Roof Replacement Revitalizes Bank Branch
- Alliant Roofing – Commercial Metal Roof Acrylic Coatings Service
- Alliant Roofing – Elevate Certified
- Rolled Steel Products – Metal Roofing Panels
- Metal Sales – Commercial Metal Roofing Systems
- Alliant Roofing – Commercial TPO Roofing Systems Guide.